Subproject 4
Chair of Metal Forming and Casting (UTG)
TP 4
-
Interactions of thermal phenomena with the formation of adiabatic shear bands in HGSS
Initial investigations indicate a correlation between the rapid rise in temperature in the cutting zone and the formation of adiabatic shear bands (ASB) during high-speed shear cutting (HGSS). To date, there is no systematic instantaneous and in situ temperature measurement in HGSS that allows the interaction of thermal phenomena with the formation of ASB to be investigated.
Sub-project 4 therefore focuses on providing a scientifically sound answer to the question of how the maximum process temperature and thermal shocks, i.e. the temperature rate in connection with the thermal expansion, interact with the melting temperature of the sheet material and the mechanical impact shock to influence the formation of ASB (Fig. 1). The prerequisite for this is the measurement of the temperature and temperature rate over the entire HGSS process with high resolution and without delay.
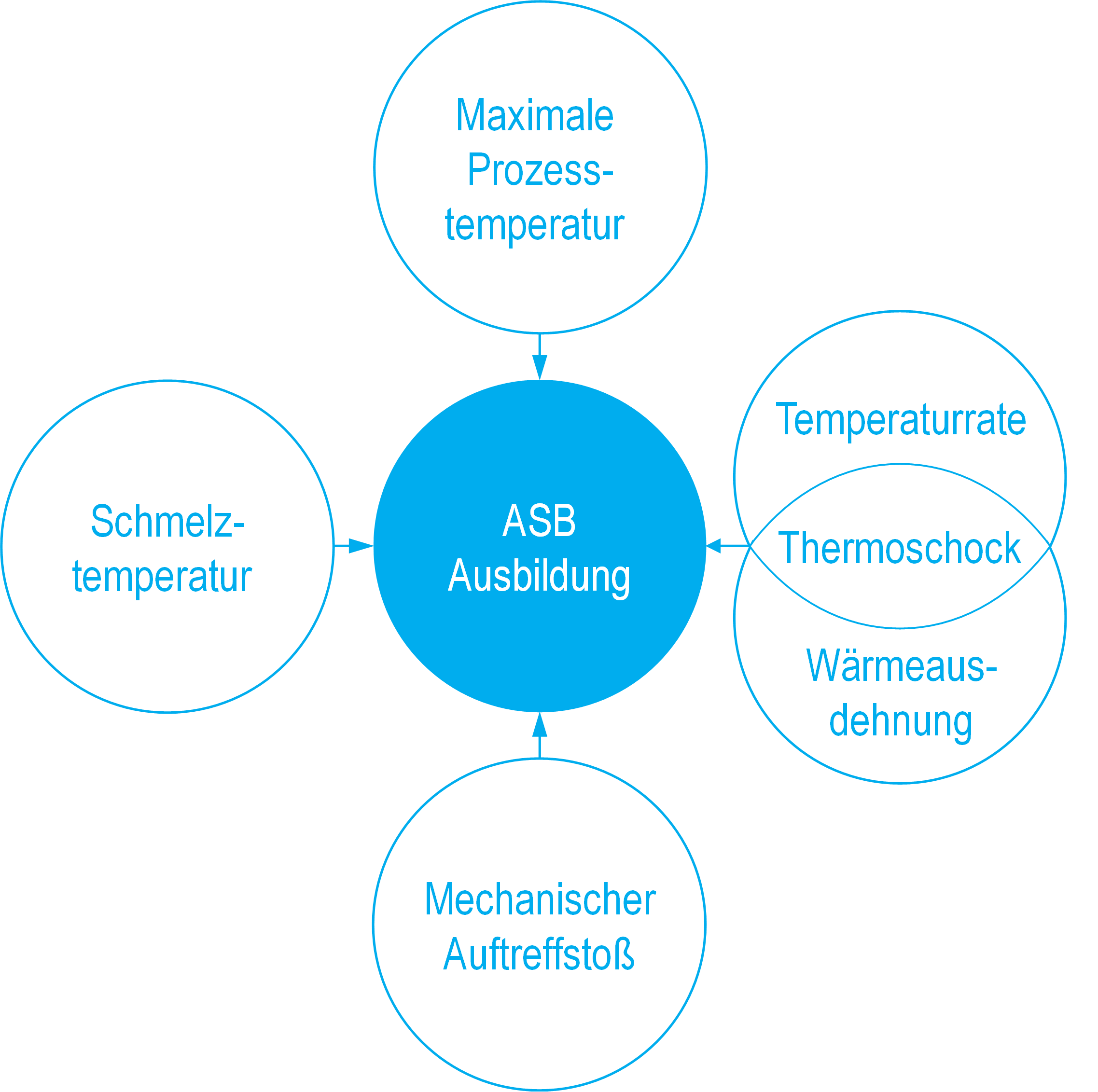
Figure 1. Research hypothesis of SP4.
In SP4, gating speeds of up to 1 m/s are considered in order to determine the material and process parameter-specific lower limits for the formation of adiabatic shear bands. A mould for use on conventional high-speed presses is being designed for this purpose. This should enable temperature measurement by means of a mould-workpiece thermocouple directly at the shear zone (Fig. 2). The data is supplemented by strain and strain rate determination using a high-speed camera and optical flow method. The link between thermal shock and melting temperature is worked out with the aid of cutting tests on low-melting materials at very high strain rates.
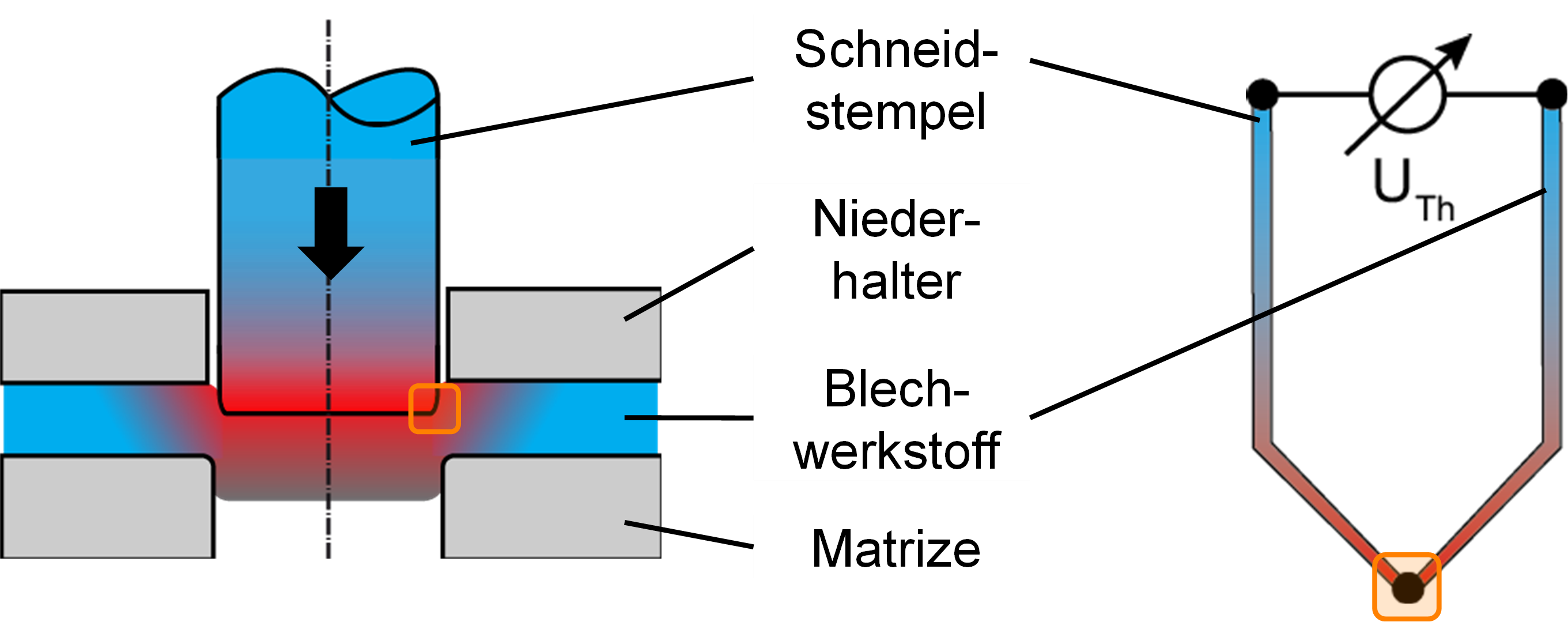
Figure 2. In situ temperature measurement during shear cutting.
The temperature data recorded in SP4 serve as an input variable for the process simulation and for investigating heat conduction phenomena. With the help of the cutting results in the lower strain rate range and a close link with the other sub-projects of the research group, the results enable the modelling for the description of the lower process limits for the formation of ASB and the targeted adjustment of the cut surface.
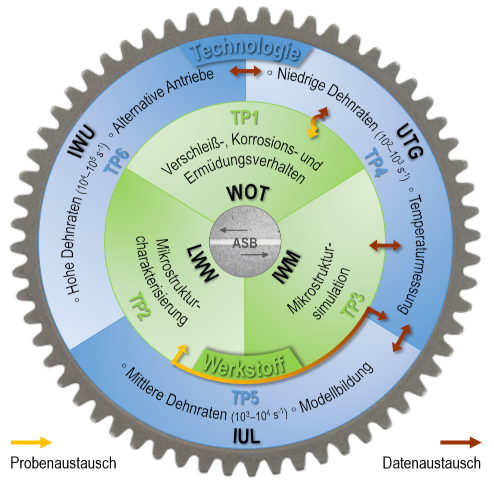
Networking diagram of TP4 with the most important sample and data exchange paths