Subproject 6
Fraunhofer Institute for Machine Tools and Forming Technology (IWU)
TP 6
-
High-speed cutting with electromagnetically accelerated tools for the production of functional surfaces at very high expansion rates
The formation of adiabatic shear bands (ASB) during high-speed shear cutting (HGSS) depends both on the process parameters - especially the forming speed - and on the mechanical and thermal properties of the material to be cut. As the forming speed increases, the shear band width decreases, especially if the heat dissipation from the shear zone is hindered by a low to moderate thermal conductivity of the material, thus favouring the adiabatic character of the deformation. In HGSS with very high forming speeds (10⁴/s to 10⁵/s), particularly narrow adiabatic shear bands (ASB) are therefore expected, which lead to minimal influence on the surrounding microstructure and to cut surfaces with unique properties. Such high forming speeds make it possible to initiate ASBs even in materials with good thermal conductivity, such as aluminium alloys, and to characterise them in terms of materials science (Figure 1) as well as to make the resulting advantages in terms of cut surface properties usable for production technology. However, existing HGSS machines are limited to maximum speeds of 10m/s, which, with typical semi-finished product thicknesses in the order of a few millimetres, lead to strain rates ≤10⁴/s and thus to relatively wide shear zones, especially in materials with good thermal conductivity.
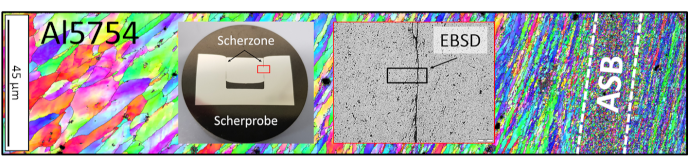
Figure 1. EBSD image of the shear zone of a 5000 aluminium alloy shear specimen deformed at local strain rates of over 10⁴/s (IWU and LWW).
In SP6, a drive concept based on electromagnetic forces is therefore being designed, with which tool speeds of up to 25 m/s are possible, and an HGSS test rig is being developed and implemented, in which relevant process parameters such as the mass and speed of the impact body and punch, cutting gap or cutting surface length can be flexibly varied. Based on this, complementary numerical-experimental analyses of the electromagnetic and mechanical subsystems will be carried out and the influences of the impact body movement and the triaxiality in the workpiece on the cutting surface properties will be investigated. These investigations will then be used to identify process parameters with which particularly thin ASBs can be produced both in materials with moderate thermal conductivity (e.g. high-strength steels) and in materials with high thermal conductivity (e.g. aluminium alloys). Finally, an energy balance of the process is to be carried out, which forms the basis for the prospective design of particularly energy-efficient HGSS processes with reduced equipment load.
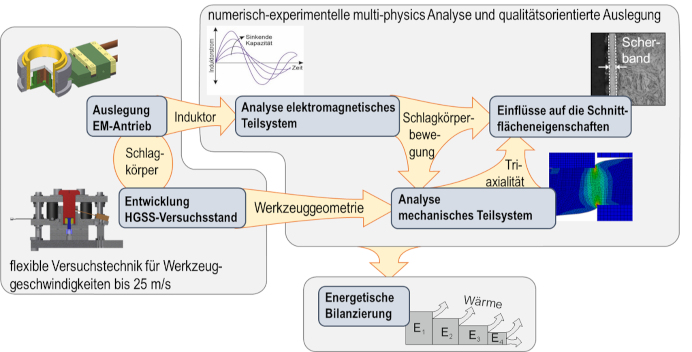
Figure 2. Methodological approach to the investigation of HGSS with electromagnetically accelerated tools for the production of functional surfaces at very high strain rates.
Within the research group, SP6 covers the investigation of the highest speed and strain rate range. The generated cut surfaces enable the material-technical investigations in SP1 and SP2 and the validation of the numerical investigations in SP3. The comparison of the results from SP6 with the results of the investigations on HGSS at low and medium forming speeds (SP4 and SP5) allows a complete picture of the decisive influences on ASB formation.
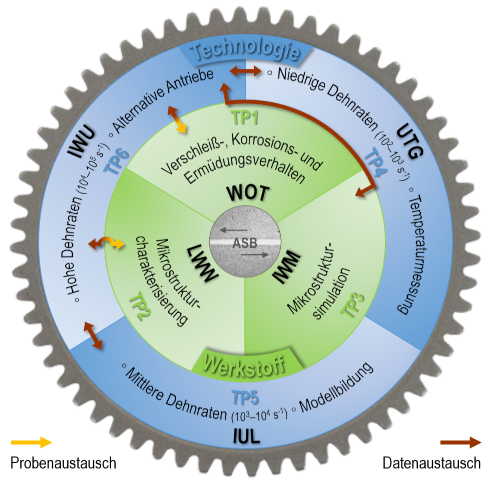
Networking diagram of TP6 with the most important sample and data exchange paths