Subproject 5
Institute for Forming Technology and Lightweight Components (IUL)
TP 5
-
Adjustment of the properties of non-rotationally symmetrical sheet metal components by high-speed shearing
The research in this sub-project makes it possible to utilise the cut surfaces of generally asymmetrical, initially non-rotationally symmetrical, components as functional surfaces. The aim of the project is to describe the influence of the process parameters during high-speed shearing (HGSS) on the properties of non-rotationally symmetrical sheet metal parts. Methods for the targeted influencing of component properties via changes in the stress state, taking into account the material properties, are being developed. In particular, the generation of an adiabatic shear band in the cutting zone to utilise the cutting edge as a functional surface is being investigated.
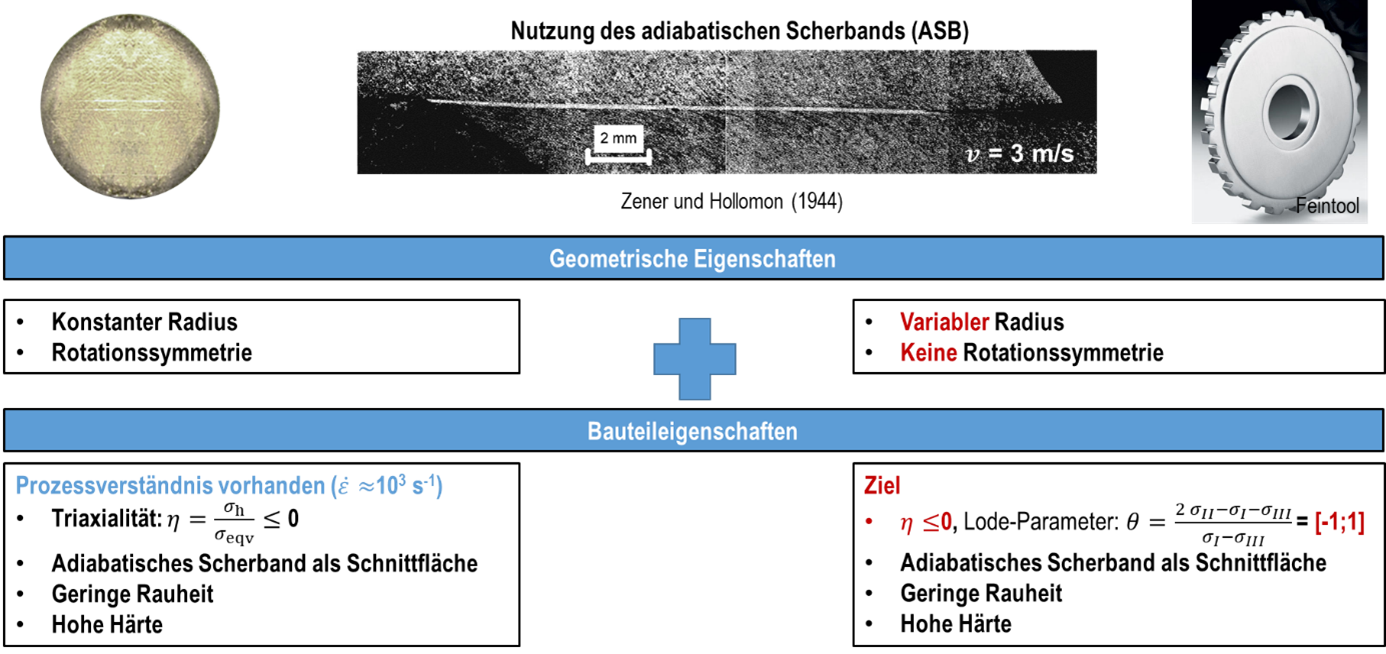
Figure 1. Aim of the investigations.
Shear band formation depends on the material properties, the stress state and the thermo-mechanical boundary conditions (strain rate, temperature). In HGSS, the imposed thermo-mechanical boundary conditions are significantly determined by the process parameters (geometry of workpiece and tool, energy, punch speed) and the stress state. Previous investigations have essentially established correlations between cutting gap and cutting surface parameters for rotationally symmetrical components (lode parameters equal to zero). The focus of the TP is on influencing the stress state in the HGSS to adjust the properties of non-rotationally symmetrical (non-zero Lode parameters) components (see Figure 1).
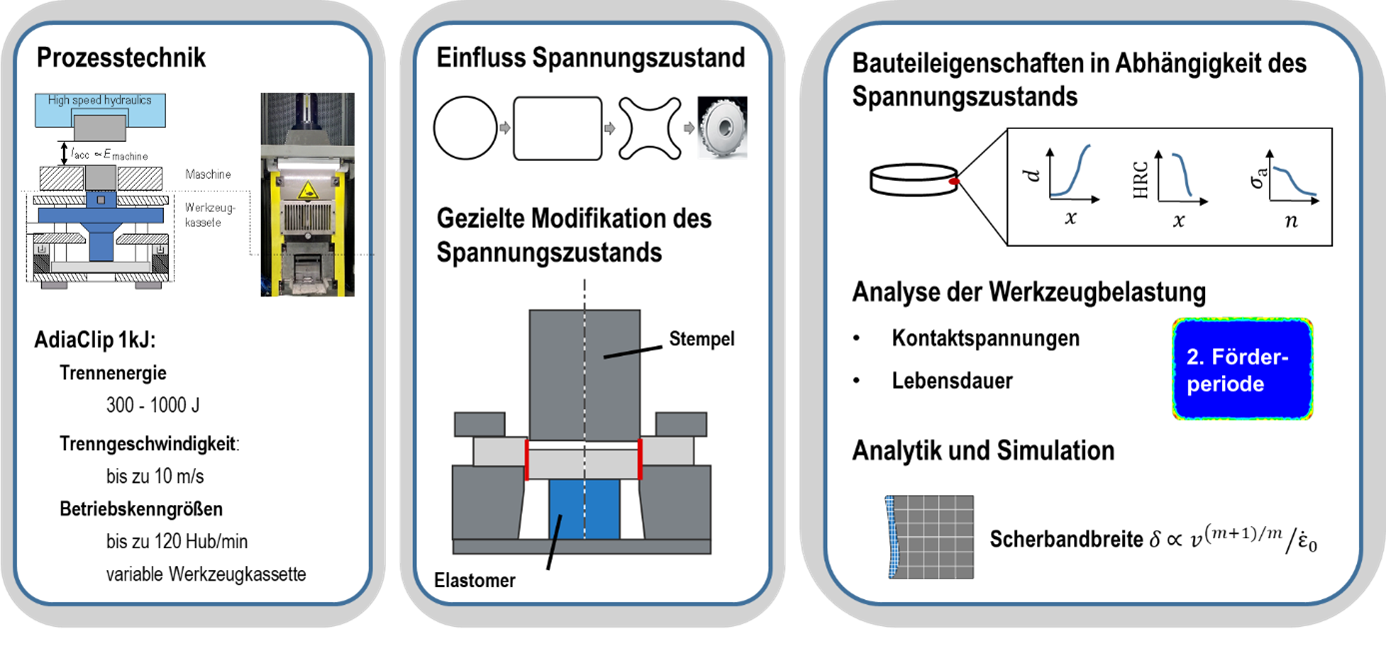
Figure 2. Methodological approach.
The tests at the IUL in Dortmund are carried out on the AdiaClip 1kJ energy-bound hydraulic press. Components with increasing degrees of asymmetry, e.g. with changing radii of curvature, are manufactured using HGSS (cutting speeds of up to 10 m/s). The cut surface properties are determined in co-operation with the other TPs and correlated with the stress state. The stress state is determined using finite element simulations, which are validated using strain measurements on the cut surface.
Based on these results, the tools are modified (chamfering of the punch, introduction of an embossing step, elastomer cushion under the component) in order to superimpose compressive shear stresses that favour the formation of adiabatic shear bands. The materials under investigation are the steels 22MnB5 (hardened), C60 (hardened) and the aluminium alloy EN AW-5754. The relevant properties of the functional surface are hardness, residual stresses, corrosion properties and service life. The influence of the process parameters on tool life is being determined in preparation for a second funding period.
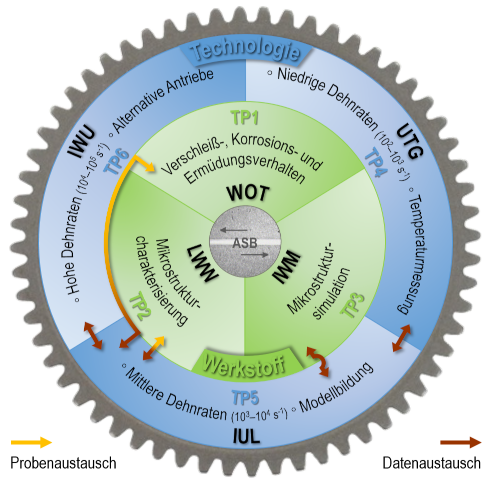
Networking diagram of TP5 with the most important sample and data exchange paths