Subproject 1
Chair of Materials and Surface Technology (WOT)
TP 1
-
Wear, corrosion and fatigue behaviour of HGSS functional surfaces
Depending on the material and the selected process parameters, cut surfaces produced by high-speed shear cutting (HGSS) can contain adiabatic shear bands (ASB). These are homogeneous zones that are clearly microstructurally separated from the base material and have a significantly different property profile compared to the surrounding material, such as a higher hardness. However, the structure-property relationships of HGSS interfaces have so far been largely unexplored. The focus of sub-project 1 is therefore to provide a scientifically sound answer to the question of how HGSS interfaces behave under tribological, corrosive and cyclic mechanical loads (Fig. 1). This is directly linked to the need to gain a fundamental understanding of the mechanisms involved and thus the identification of process-microstructure-property relationships. The prerequisite for this is the interpretation of the results of the wear, corrosion and fatigue tests, i.e. the correlation of the determined cut surface properties with the process parameters and the resulting microstructure, which must be carried out in coordination with the research group partners.
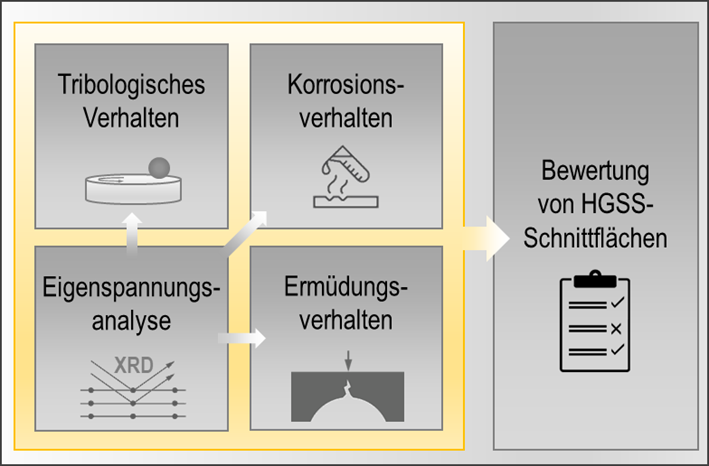
Figure 1. Schematic representation of the work programme of SP1.
The tribological investigations include various wear tests that depict different load regimes. The material behaviour of both flat and curved HGSS interfaces is systematically investigated under furrowing, sliding and rolling loads with and without an intermediate medium. The corrosion behaviour is characterised across scales. On the one hand, the macroscopic behaviour is determined in immersion and salt spray tests. On the other hand, the corrosion resistance of individual structural components of the ASB and the surrounding material is assessed comparatively using a microcorrosion cell (Fig. 2). Specially designed sample geometries are also used to investigate the fatigue properties of ASB, which were generated in a wide strain rate range (10²-10⁵ s⁻¹). In addition, the residual stresses of HGSS interfaces are measured by X-ray diffraction (XRD) to assess the material behaviour. The macro and micro residual stresses determined in this way are used to interpret the results of the tribological, corrosive and cyclic mechanical tests and also represent important evaluation and validation parameters for the project partners' microstructure modelling and process simulation.
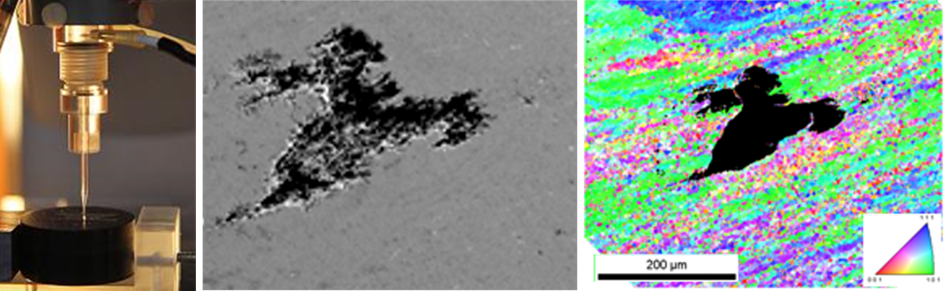
Figure 2. Microcorrosion cell (left) and localised corrosion in a shear band in AlMgSi0.5 (centre & right).
The research results obtained in SP1 form the basis for evaluating the performance characteristics and thus the practical suitability of HGSS interfaces. By providing feedback to the other sub-projects, the results also make it possible to directly influence the design of the HGSS process and thus specifically adjust the properties of the functional surface.
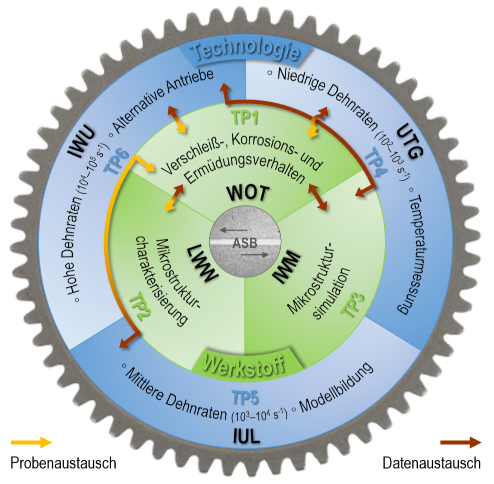
Networking diagram of TP1 with the most important sample and data exchange paths