With high speed to efficient production chains in sheet metal parts production
After one year, the DFG research group "FUNDAM³ENT", coordinated by Chemnitz University of Technology, draws a positive interim balance for research into more efficient methods of metal production for products in areas such as electrical and medical technology or the automotive industry
As part of the second status seminar of the programme funded by the German Research Foundation (DFG) Research group (FOR) " Functional surfaces through adiabatic high-speed processes: Microstructure, mechanisms and model development - FUNDAM³ENT ", project managers and other participants in FOR "FUNDAM³ENT" drew an extremely positive interim conclusion. The seminar took place from 18 to 19 September 2023 at the Fraunhofer Institute for Machine Tools and Forming Technology (IWU) in Chemnitz. The semi-annual status seminars serve as a forum for mutual exchange within the consortium and for strategic planning of further research work.
"Thanks to the committed cooperation of all those involved and the pooling of expertise from materials science, materials engineering and production technology, the first interesting research results have already been presented to the specialist public at conferences such as 'FEMS EUROMAT 2023'. The involvement of international guest scientists and the participation of students in various tasks of the research group can also be seen as an important success. These results create the basis for further targeted work on scientific issues," summarises Prof Dr Thomas Lampke , owner of the Chair of Materials and Surface Technology (WOT) at Chemnitz University of Technology (TUC) and spokesperson for the FOR.
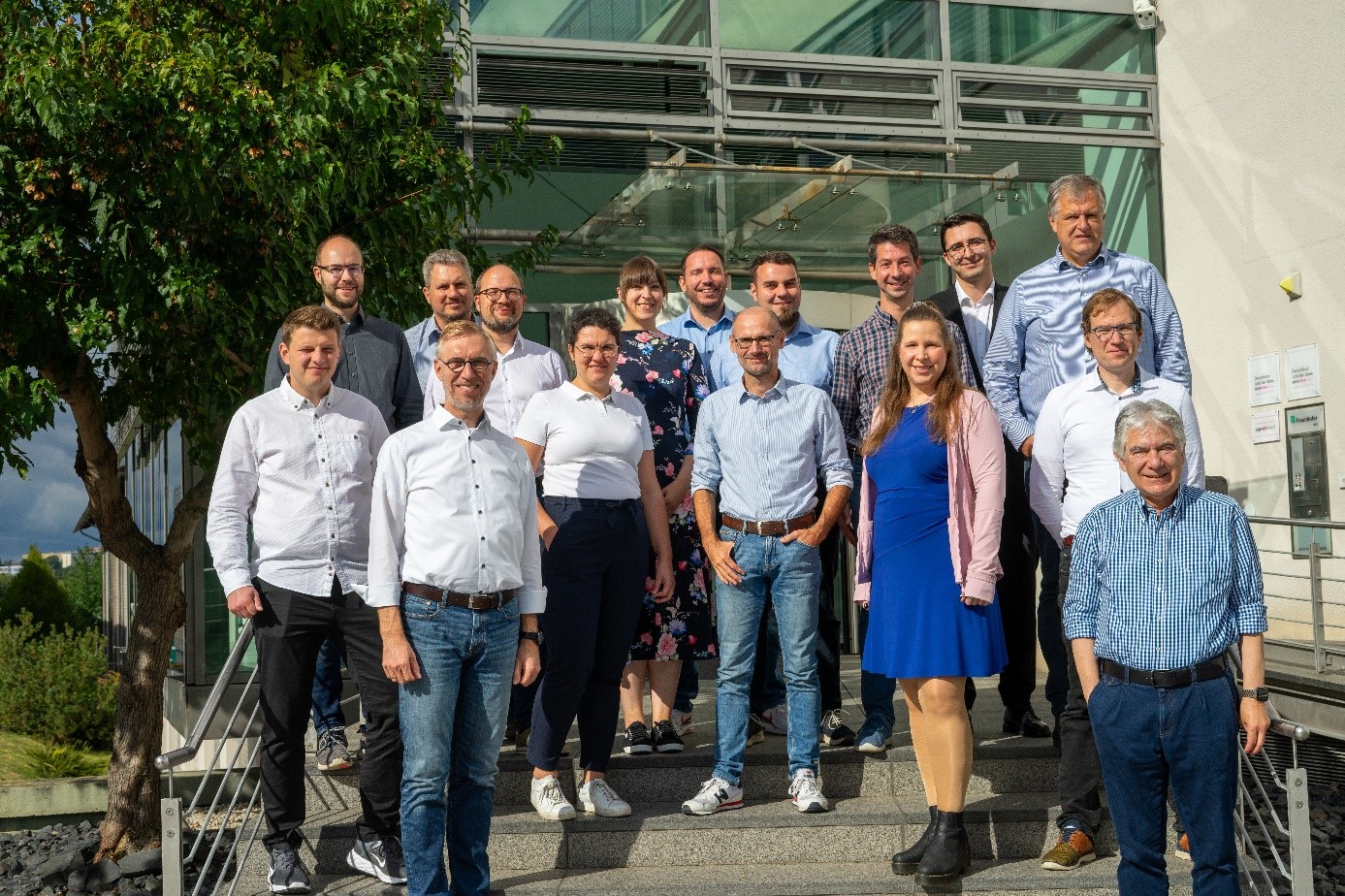
Sub-project leaders and members of the FUNDAM³ENT research group at the second status seminar at the Fraunhofer Institute for Machine Tools and Forming Technology (IWU) in Chemnitz. In the picture from left: Olaf Schrage (IUL, TU Dortmund), Mario Scholze (LWW, TUC), Frank Huberth (back: FhG IWM, Freiburg), Thomas Lampke (WOT, TUC), Rico Drehmann (WOT, TUC), Katja Holzer (UTG, TU Munich), Lisa Winter (WOT, TUC), Sven Winter (IWU Chemnitz), Alexander Butz (IWM Freiburg), Maik Linnemann (IWU Chemnitz), Martin Wagner (LWW, TUC), Verena Psyk (IWU Chemnitz), Elmar Galiev (IWU Chemnitz), Wolfgang Volk (UTG, TU Munich), Till Clausmeyer (IUL, TU Dortmund), A. Erman Tekkaya (IUL, TU Dortmund)
Finding more efficient ways to process and produce sheet metal components
Since the start of the FOR in September 2022, the consortium has been working on the exciting question of the conditions under which high-speed shear cutting (HGSS) can be used to produce cut surfaces on sheet metal that are characterised by particularly low roughness, burr-free edges and high hardness. Conventional shear cutting is primarily used in the large-scale production of sheet metal components. This covers a broad spectrum from the smallest parts for electrical or medical technology to machine elements such as perforated sheets or sprockets through to vehicle doors for the automotive industry.
Researchers presented the progress of the six sub-projects on site. The intensive discussion that followed sharpened the focus for the extensive research questions of the DFG research group. The research work to date shows that the adiabatic shear bands (ASB) in the cut surface, which only occur at high deformation speeds, obviously play an important role here.
Research data management in open source format
There was also a constructive dialogue on the topic of research data management. The fact that a separate data management instance based on the open-source system "openBIS" was installed for this purpose shows the particular importance with which this aspect is treated in the research group. the integration of electronic laboratory notebooks and the processing of data across research centres means that the international FAIR principles, according to which data can be found ( F indable),accessible ( A ccessible), I nteroperable and reusable ( R eusable) should be taken into account. In this way, the FOR is committed to complying with the guidelines for safeguarding good scientific practice, while also making a significant contribution to the sustainable and resource-efficient handling of data through the reusability of data for future research projects, thereby addressing a topic that is becoming increasingly important due to the exponentially growing volume and increasing complexity of research data.The consistent collection and meaningful structuring of data is the prerequisite for its interoperability and thus a decisive basis for gaining new insights in the future through machine learning methods and the use of artificial intelligence.
Innovative system for fresh research impetus
The status seminar was rounded off with a demonstration of two HGSS systems in the test field of the Fraunhofer Institute for Machine Tools and Forming Technology (IWU). In addition to a hydraulically driven HGSS system, a new type of system accelerated by an electromagnetic pulse was also used, with which significantly higher cutting speeds can be achieved. This in turn is an important prerequisite for the formation of ASB, particularly in materials with good thermal conductivity.
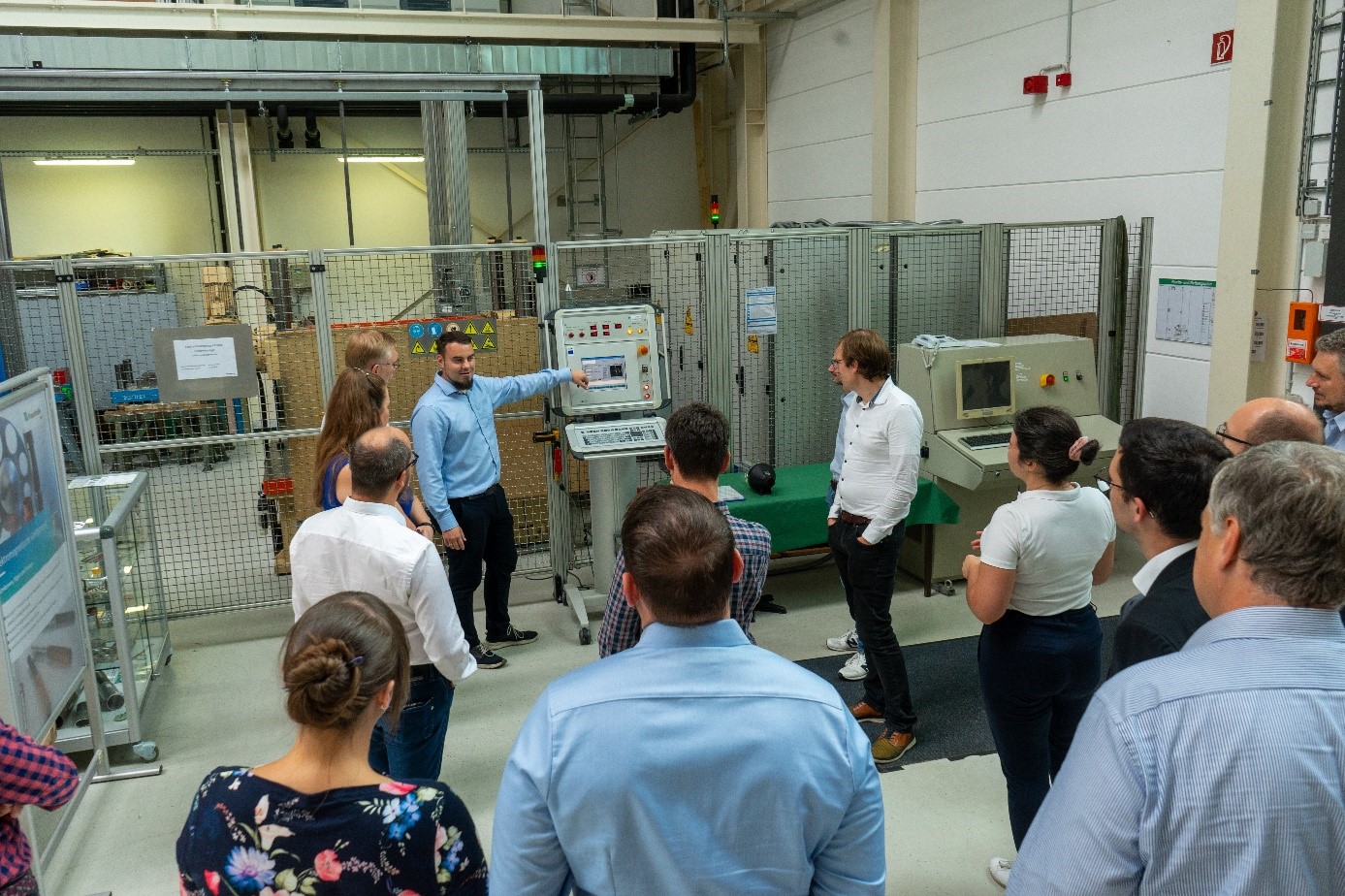
Dr Maik Linnemann from the Fraunhofer Institute for Machine Tools and Forming Technology (IWU) demonstrating an HGSS system.
The new and further development of hydraulically and electromagnetically driven cutting tools and the commissioning of a newly designed tribometer holder with the associated measuring technology for wear analyses of HGSS cutting surfaces will be among the most important tasks in the coming weeks and months.
The organisation of a doctoral seminar to promote young scientists and a symposium at the Materials Science and Engineering Congress (MSE) 2024 in Darmstadt are also on the agenda. At the same time, the participants are promoting cooperation with various international experts through guest visits to the institutions involved in the research group.
Background: Research group " FUNDAM³ENT “
The DFG is funding FOR FUNDAM³ENT with around 3.72 million euros in the first four-year funding period - of which around 1.54 million euros will go to Chemnitz University of Technology. The spokesperson is Prof Dr Thomas Lampke, Chair of Materials and Surface Technology at the TUC.
The focus of the research is the systematic investigation of the various material and process-related factors influencing the formation of ASB in HGSS. Ideally, energy-intensive post-processing steps that were previously necessary can be eliminated, significantly shortening the process chain for sheet metal part production. From both an economic and ecological point of view, this opens up great potential for a wide range of materials, from light metals such as aluminium to high-strength steels.
The consortium includes scientists from TU Munich, the Fraunhofer Institute for Mechanics of Materials (IWM) in Freiburg, TU Dortmund University, the Fraunhofer Institute for Machine Tools and Forming Technology (IWU) as well as the Chair of Materials and Surface Technology and the Chair of Materials Science at the TUC.
Further information are available online: http://www.for-5380.de
Contact: Dr Rico Drehmann, Tel. 0371 531-39331, E-Mail rico.drehmann@mb.tu-chemnitz.de and Prof Dr Thomas Lampke, Tel. 0371 531-36163, e-mail thomas.lampke@mb.tu-chemnitz.de